Common Problems and Solutions for Pressure Pump Adjustment
Proper pressure pump adjustment is essential for ensuring efficient and reliable performance of hydraulic systems. A pressure pump is a critical component of any hydraulic system, and it is responsible for delivering fluid at a specific pressure to drive other components. A poorly adjusted pressure pump can lead to system failure, decreased efficiency, and increased energy consumption. Therefore, it is crucial to understand the importance of pressure pump adjustment and how it impacts system performance.The purpose of this paper is to provide an overview of pressure pump adjustment, including its definition, different types of adjustment techniques, and factors that influence adjustment. The paper will also cover common problems faced during pressure pump adjustment, solutions for these problems, and pressure pump adjustment in different applications. Additionally, the paper will discuss pressure pump adjustment technology trends, challenges and limitations of pressure pump adjustment techniques, and future outlook.
Overall, this paper aims to provide a comprehensive understanding of pressure pump adjustment and its importance in hydraulic systems. By the end of this tutorial, readers will have a better understanding of the factors that influence pressure pump adjustment, the common problems that arise during adjustment, and the solutions to these problems. The information presented in this paper can be used to ensure the proper adjustment and maintenance of pressure pumps, leading to improved system performance, energy efficiency, and cost savings.
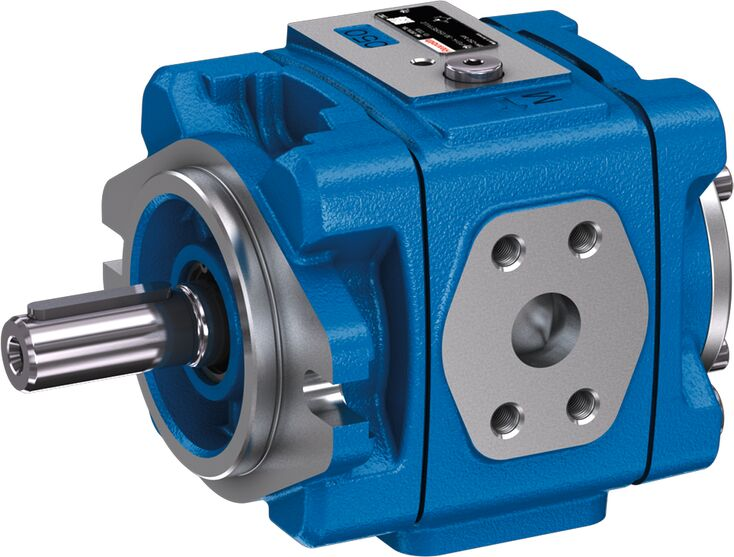
Understanding Pressure Pump Adjustment
Definition of Pressure Pump Adjustment:
Pressure pump adjustment refers to the process of adjusting the pressure at which a pump delivers fluid to other components in a hydraulic system. The adjustment process typically involves setting the pressure to a specific value, which is determined by the requirements of the system.
Different Types of Pressure Pump Adjustment Techniques:
There are several different techniques for adjusting the pressure of a hydraulic pump. The most common methods include:
-
Manual Adjustment: Manual adjustment involves adjusting the pressure of a pump using a manual control valve. This method is simple and cost-effective, but it requires manual intervention, which can be time-consuming.
-
Electronic Adjustment: Electronic adjustment involves using electronic sensors to adjust the pressure of a pump automatically. This method is more efficient than manual adjustment, but it requires additional equipment and is more expensive.
-
Variable Displacement Pumps: Variable displacement pumps are designed to automatically adjust the pressure based on the load of the system. This method is highly efficient, but it requires specialized equipment and can be expensive.
Factors that Influence Pressure Pump Adjustment:
Several factors can influence the pressure pump adjustment process, including:
-
System Load: The load of a hydraulic system can have a significant impact on the pressure required to operate the system effectively. A system with a high load may require higher pressure than a system with a low load.
-
System Flow: The flow rate of a hydraulic system can also impact pressure pump adjustment. A system with high flow rates may require higher pressure than a system with low flow rates.
-
Fluid Viscosity: The viscosity of the fluid being pumped can impact the pressure required to operate the system effectively. A system pumping thicker fluids may require higher pressure than a system pumping thinner fluids.
Overall, understanding pressure pump adjustment is critical for ensuring the efficient and reliable operation of hydraulic systems. Different types of adjustment techniques are available, and the selection of the appropriate technique depends on several factors, including system load, system flow, and fluid viscosity.
Common Problems Faced in Pressure Pump Adjustment
Despite the importance of proper pressure pump adjustment, several problems can arise during the adjustment process. Some of the common problems include:
-
Pressure Fluctuation: Pressure fluctuations occur when the pressure delivered by the pump varies over time, causing inconsistent system performance. This problem can occur due to a variety of factors, including system load, fluid viscosity, and pump wear.
-
Overheating: Overheating can occur when the pressure in the system is too high, leading to increased friction and heat generation. This problem can cause system failure, decreased efficiency, and increased energy consumption.
-
Cavitation: Cavitation occurs when air bubbles are formed in the fluid being pumped, leading to decreased efficiency and increased wear on the pump. This problem can occur due to a variety of factors, including improper fluid selection, pump wear, and inadequate fluid levels.
-
Leakage: Leakage occurs when fluid escapes from the hydraulic system, leading to decreased system performance and potential system failure. This problem can occur due to a variety of factors, including pump wear, damaged seals, and improper installation.
-
Noise: Noise can occur when the pressure in the system is too high, leading to increased vibration and sound generation. This problem can cause annoyance and potential hearing damage to operators.
These problems can have a significant impact on the performance and efficiency of hydraulic systems, leading to increased energy consumption, decreased efficiency, and potential system failure. Therefore, it is crucial to identify and address these problems as quickly as possible to ensure the proper operation of the system.
Solutions for Common Pressure Pump Adjustment Problems
Several solutions can be used to address common problems faced during pressure pump adjustment. Some of these solutions include:
-
Pressure Relief Valves: Pressure relief valves can be installed to prevent pressure from exceeding a certain level, preventing overheating and other related problems. These valves can also help prevent damage to the system and prolong the lifespan of the pump.
-
Proper Fluid Selection: Proper fluid selection is critical for preventing cavitation and other related problems. The fluid should be selected based on the specific requirements of the system, including viscosity, temperature range, and compatibility with system components.
-
Regular Maintenance: Regular maintenance, including inspections, cleaning, and replacement of worn parts, can help prevent and address common problems faced during pressure pump adjustment. This maintenance should be performed on a regular schedule to ensure the proper operation of the system.
-
Professional Repair: Professional repair services can be used to address more severe problems, including pump wear, damaged seals, and improper installation. These services can help prevent system failure and ensure the proper operation of the system.
By implementing these solutions, operators can address common problems faced during pressure pump adjustment and ensure the proper operation of hydraulic systems. It is important to identify and address these problems as quickly as possible to prevent further damage to the system and maintain optimal efficiency.
Pressure Pump Adjustment in Different Applications
Pressure pump adjustment is used in a variety of applications, including industrial processes, HVAC systems, and water treatment systems. Here are some examples of pressure pump adjustment in different applications:
-
Industrial Processes: Pressure pump adjustment is used in various industrial processes to control the flow and pressure of fluids. This includes applications such as hydraulic presses, injection molding machines, and metalworking equipment. By adjusting the pressure of the fluid, operators can control the speed and force of the equipment, ensuring consistent and precise operation.
-
HVAC Systems: Pressure pump adjustment is used in HVAC systems to control the flow and pressure of air and water. This includes applications such as air handlers, chillers, and boilers. By adjusting the pressure of the air or water, operators can control the temperature and humidity of the environment, ensuring optimal comfort and energy efficiency.
-
Water Treatment Systems: Pressure pump adjustment is used in water treatment systems to control the flow and pressure of water. This includes applications such as reverse osmosis systems, filtration systems, and chemical treatment systems. By adjusting the pressure of the water, operators can ensure optimal performance and efficiency of the treatment process, ensuring high-quality water output.
In each of these applications, pressure pump adjustment is critical for ensuring optimal system performance and efficiency. By controlling the pressure and flow of fluids, operators can ensure consistent and precise operation, prevent system failure, and reduce energy consumption.
Pressure Pump Adjustment Technology Trends
Advancements in pressure pump adjustment technology are focused on improving the efficiency, reliability, and precision of hydraulic systems. Here are some of the latest trends in pressure pump adjustment technology:
-
Digital Control Systems: Digital control systems allow for precise and efficient control of pressure and flow in hydraulic systems. These systems use sensors and actuators to monitor and adjust pressure and flow, ensuring optimal performance and efficiency.
-
Variable Frequency Drives: Variable frequency drives allow for the precise control of motor speed, enabling operators to adjust pressure and flow to meet specific system requirements. These drives can reduce energy consumption and improve efficiency by adjusting the motor speed to match the load requirements of the system.
-
Predictive Maintenance: Predictive maintenance uses data analysis and machine learning algorithms to identify potential issues before they occur, allowing for proactive maintenance and repair. By monitoring system performance and detecting anomalies, operators can address potential problems before they cause system failure or decreased efficiency.
-
IoT Integration: IoT integration allows for remote monitoring and control of hydraulic systems, enabling operators to monitor and adjust pressure and flow from anywhere. By connecting hydraulic systems to the internet, operators can access real-time data and make adjustments as needed, ensuring optimal performance and efficiency.
-
Energy Recovery Systems: Energy recovery systems use the energy in hydraulic fluid to generate electricity, reducing energy consumption and improving efficiency. These systems can be used in applications such as heavy machinery and industrial processes, where large amounts of hydraulic fluid are used.
These trends in pressure pump adjustment technology are aimed at improving the efficiency and reliability of hydraulic systems, while reducing energy consumption and maintenance costs. By incorporating these technologies into hydraulic systems, operators can ensure optimal performance and efficiency, while reducing the environmental impact of hydraulic systems.
Challenges and Limitations of Pressure Pump Adjustment Techniques
Despite the benefits of pressure pump adjustment, there are some challenges and limitations to consider. Some of the common challenges and limitations include:
-
Complex Systems: Hydraulic systems can be complex, requiring specialized knowledge and skills to design, install, and maintain. Improper adjustment or maintenance can result in system failure or decreased efficiency.
-
Maintenance Requirements: Hydraulic systems require regular maintenance, including inspections, cleaning, and replacement of worn parts. Failure to perform proper maintenance can lead to decreased system performance and efficiency.
-
High Cost: Hydraulic systems can be expensive to design, install, and maintain, particularly for large or complex systems. This cost can be a barrier to entry for some industries, limiting the adoption of hydraulic systems.
-
Environmental Impact: Hydraulic systems can have a negative environmental impact, particularly if they are not designed or maintained properly. Fluid leaks, system failures, and inefficient operation can result in environmental damage and increased carbon emissions.
-
Compatibility Issues: Hydraulic systems must be compatible with the fluids, components, and materials used in the system. Incompatible components or fluids can result in system failure or decreased efficiency.
To address these challenges and limitations, operators can implement proper training and maintenance programs, use compatible components and fluids, and consider the environmental impact of hydraulic systems. By addressing these challenges and limitations, operators can ensure the proper operation and efficiency of hydraulic systems, while reducing their environmental impact.
Future Outlook
The future of pressure pump adjustment looks promising, with continued advancements in technology and growing demand for more efficient and sustainable hydraulic systems. Some potential future developments in pressure pump adjustment technology and applications include:
-
Automation: Automation of hydraulic systems could improve efficiency, reduce maintenance requirements, and increase safety. Automated systems could use machine learning algorithms to adjust pressure and flow in real-time, optimizing system performance and reducing energy consumption.
-
Energy Storage: Energy storage systems could be integrated with hydraulic systems, allowing operators to store energy during periods of low demand and use it during periods of high demand. This could reduce energy consumption and improve system efficiency.
-
Smart Sensors: Smart sensors could be used to monitor system performance and detect potential issues before they occur. These sensors could be integrated with IoT systems, allowing operators to monitor and adjust pressure and flow remotely.
-
Lightweight Materials: The use of lightweight materials, such as carbon fiber, could reduce the weight and cost of hydraulic systems, while increasing efficiency.
-
Sustainable Fluids: The use of sustainable fluids, such as vegetable oils or biodegradable hydraulic fluids, could reduce the environmental impact of hydraulic systems.
These potential future developments in pressure pump adjustment technology and applications could have a significant impact on industries and society as a whole. By improving the efficiency and sustainability of hydraulic systems, these developments could reduce energy consumption, lower maintenance costs, and decrease the environmental impact of hydraulic systems.