Hydraulic Pump Types and Their Applications: A Comprehensive Overview
Hydraulic pumps play a crucial role in many industries and systems, ranging from construction equipment to manufacturing and transportation. It is important to understand the different types of hydraulic pumps and their applications in order to select the most appropriate pump for a specific system or application. This paper provides an overview of hydraulic pumps, including their function, components, and types. It also explores the applications of hydraulic pumps in different industries and systems, as well as the advantages and limitations of different hydraulic pump types. The paper concludes with a discussion on potential future developments in hydraulic pump technology and their potential impacts on industries and society as a whole.
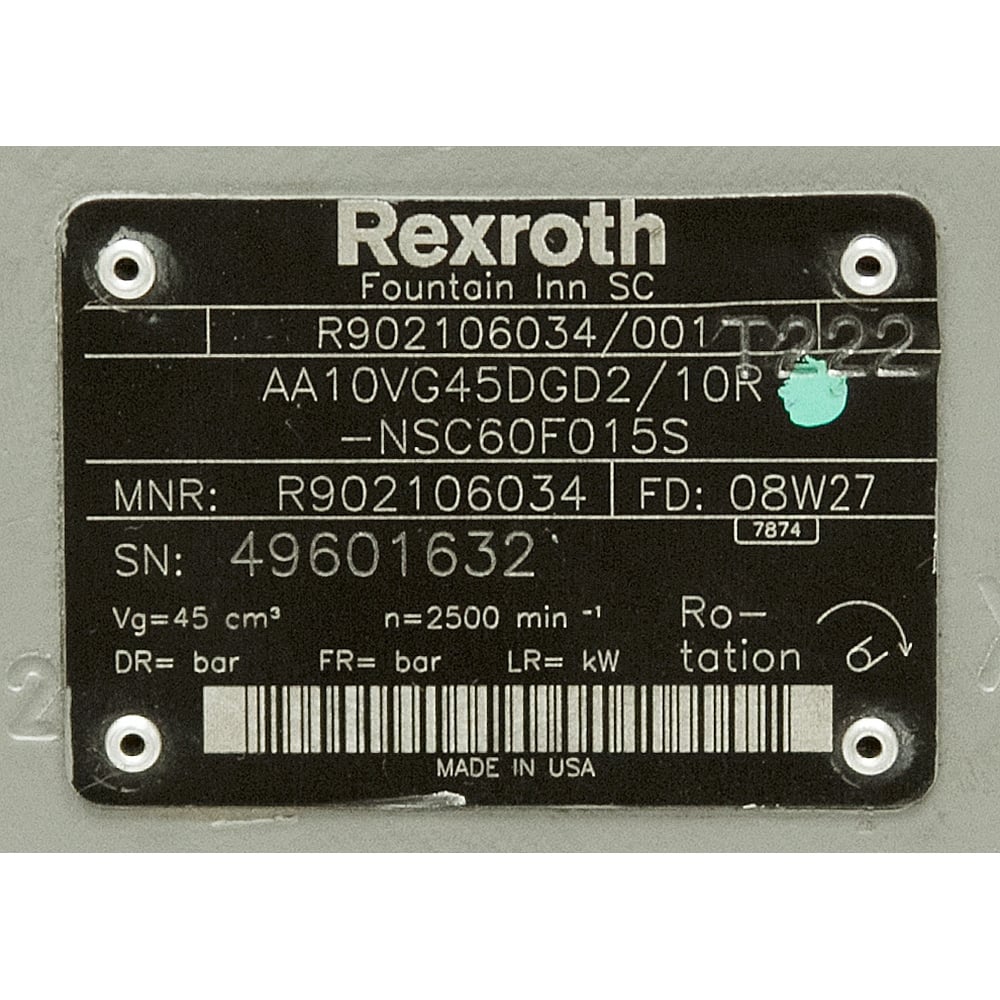
Understanding Hydraulic Pumps
Hydraulic pumps are mechanical devices that convert mechanical energy into hydraulic energy in the form of flow and pressure. They are essential components of hydraulic systems used in various industries, including construction, manufacturing, and transportation. Understanding hydraulic pumps is crucial in ensuring that the hydraulic system operates efficiently and safely.
A hydraulic pump typically consists of a hydraulic motor, a reservoir, a pump, and hydraulic lines. Hydraulic pumps are responsible for producing flow and pressure in hydraulic systems, which are used to power hydraulic cylinders, motors, and other hydraulic components. There are several types of hydraulic pumps, including gear pumps, vane pumps, and piston pumps.
The choice of hydraulic pump depends on several factors, including the flow rate, pressure, and viscosity of the fluid, as well as the operating temperature and the overall system design. Each type of hydraulic pump has its advantages and disadvantages, and the selection criteria depend on the specific application.
In addition to understanding the different types of hydraulic pumps, it is also essential to understand their operating principles. For example, piston pumps use a reciprocating piston to generate flow and pressure, while gear pumps use meshing gears to transfer fluid. Vane pumps, on the other hand, use a rotating cam with vanes to create flow and pressure.
Understanding the function and components of hydraulic pumps is crucial in selecting the right type of pump for a specific application. By selecting the right pump and operating it correctly, hydraulic systems can operate efficiently and reliably, reducing downtime and maintenance costs.
Types of Hydraulic Pumps and Their Operating Principles
Hydraulic pumps are used in a variety of applications to generate high-pressure fluid flow for the operation of hydraulic systems. There are several types of hydraulic pumps available, each with its own unique operating principles and advantages. In this section, we will discuss the different types of hydraulic pumps and their operating principles.
-
Piston Pumps Piston pumps are one of the most common types of hydraulic pumps. They are known for their high pressure and high flow rates, making them ideal for heavy-duty applications. The pump consists of a cylinder, piston, inlet valve, and outlet valve. The piston moves back and forth in the cylinder, drawing fluid in through the inlet valve and pushing it out through the outlet valve. The piston can be driven by a variety of methods, including a cam, crankshaft, or electric motor.
-
Gear Pumps Gear pumps are another popular type of hydraulic pump. They are simple in design and consist of two meshing gears that rotate in opposite directions. The rotation of the gears generates a flow of fluid, which is then directed to the outlet. Gear pumps are known for their reliability and long service life, making them ideal for a wide range of applications.
-
Vane Pumps Vane pumps are similar to gear pumps in that they consist of a rotor and a stator. The rotor has a series of vanes that slide in and out of the stator. As the rotor rotates, the vanes move in and out, creating a vacuum that draws fluid into the pump. The fluid is then forced out of the pump and directed to the outlet. Vane pumps are known for their smooth operation and low noise levels.
-
Radial Piston Pumps Radial piston pumps are another type of hydraulic pump that is commonly used in high-pressure applications. They consist of a rotor with multiple pistons that move radially in and out of the cylinder block. The rotation of the rotor drives the pistons, which generate a flow of fluid. Radial piston pumps are known for their high pressure capabilities and precise flow control.
-
Axial Piston Pumps Axial piston pumps are similar to radial piston pumps but have pistons that move axially instead of radially. They are known for their high efficiency and ability to handle high flow rates. Axial piston pumps can be further divided into two categories: swash plate and bent axis. Swash plate pumps use a swash plate to vary the angle of the pistons, while bent axis pumps use a bent axis to achieve the same effect.
Overall, the type of hydraulic pump selected for a particular application depends on the specific requirements of the system. The operating principles and advantages of each type of hydraulic pump must be carefully considered to ensure that the pump can provide the necessary flow and pressure for the system to operate efficiently.
Applications of Hydraulic Pumps
Hydraulic pumps have a wide range of applications across different industries, owing to their ability to generate high amounts of power in a relatively small size. Some of the most common applications of hydraulic pumps are:
-
Industrial Manufacturing: Hydraulic pumps are widely used in industrial manufacturing applications such as metal stamping, forging, and extrusion. They are used to power hydraulic presses, which can exert high amounts of force to shape metal into various forms.
-
Construction: Hydraulic pumps are used extensively in the construction industry to power heavy equipment such as bulldozers, excavators, and cranes. They are also used to power hydraulic jacks and lifts, which are used to lift heavy objects and move them to different locations.
-
Aerospace: Hydraulic pumps are used in the aerospace industry to power various systems, such as landing gear and flaps. They are also used to power hydraulic actuators that control the movement of aircraft control surfaces.
-
Agriculture: Hydraulic pumps are used in the agriculture industry to power various types of farm equipment such as tractors, harvesters, and plows. They are also used to power irrigation systems, which require high amounts of water to be moved over long distances.
-
Automotive: Hydraulic pumps are used in the automotive industry to power various systems such as power steering and braking. They are also used to power hydraulic lifts, which are used in automotive repair shops to lift vehicles off the ground.
-
Mining: Hydraulic pumps are used in the mining industry to power various types of equipment such as drills, loaders, and excavators. They are also used to power hydraulic shovels and crushers, which are used to extract minerals from the ground.
-
Marine: Hydraulic pumps are used in the marine industry to power various systems such as steering, thrusters, and winches. They are also used to power hydraulic cranes, which are used to load and unload cargo from ships.
Overall, hydraulic pumps play a critical role in powering a wide range of industrial applications across various industries. Their versatility, high power output, and compact size make them an essential component in many industrial systems.
Piston Pumps
Piston pumps are a type of hydraulic pump that uses reciprocating pistons to move fluid through the system. These pumps are commonly used in high-pressure applications where a high volume of fluid needs to be moved quickly. Piston pumps are available in several different designs, including axial, radial, and bent axis.
Axial piston pumps are one of the most common types of piston pumps. They consist of a number of pistons arranged in a circular pattern around a central drive shaft. As the drive shaft rotates, the pistons reciprocate in and out of their cylinders, generating flow and pressure. Axial piston pumps are highly efficient and can provide high pressures and flow rates.
Radial piston pumps, on the other hand, have pistons arranged radially around a central cam. As the cam rotates, the pistons are forced in and out of their cylinders, generating flow and pressure. Radial piston pumps are generally more compact than axial piston pumps and can be used in a wider range of applications.
Bent axis piston pumps are similar to axial piston pumps but with the drive shaft and cylinder block at an angle. This design allows for a more compact pump and a greater power-to-weight ratio. Bent axis piston pumps are commonly used in mobile equipment, such as construction machinery and agricultural vehicles.
Piston pumps are highly versatile and can be used in a wide range of applications. They are commonly used in the oil and gas industry, power generation, and construction equipment. Their ability to provide high flow rates and pressures makes them ideal for demanding applications such as hydraulic presses and heavy-duty machinery.
One of the main advantages of piston pumps is their efficiency. They can provide a high output of fluid with minimal energy input, which can result in cost savings over the long term. Additionally, piston pumps are highly reliable and can provide consistent performance over a long service life.
However, piston pumps can also be more complex and expensive than other types of hydraulic pumps. They require precise manufacturing and assembly to ensure that the pistons move smoothly and efficiently. Additionally, piston pumps can be more prone to wear and tear, which can require more frequent maintenance and replacement of parts.
In conclusion, piston pumps are a powerful and versatile type of hydraulic pump that can provide high flow rates and pressures. They are commonly used in demanding applications in a variety of industries, and their efficiency and reliability make them a popular choice for many applications. While they may be more complex and expensive than other types of pumps, their benefits can outweigh the costs in many cases.
Gear Pumps
Gear pumps are a type of hydraulic pump that uses a pair of meshing gears to generate flow. The gears are typically spur gears or helical gears, and are mounted on parallel shafts inside a housing. One gear is driven by a motor or other power source, while the other gear is driven by the meshing action of the teeth. As the gears rotate, they create chambers between the teeth that trap fluid and move it from the inlet to the outlet of the pump.
Gear pumps are known for their simplicity, reliability, and efficiency. They are able to generate high pressures and flow rates with relatively low power input, making them ideal for a wide range of applications. Some common uses for gear pumps include:
- Lubrication systems: Gear pumps are commonly used to circulate oil or other lubricants in machinery, providing lubrication to moving parts and reducing wear and tear.
- Transfer systems: Gear pumps are used to transfer fluids between tanks or containers in a wide range of industries, including chemical processing, food and beverage, and pharmaceuticals.
- Hydraulic power units: Gear pumps are often used in hydraulic power units, providing the high-pressure fluid required to operate hydraulic cylinders and motors.
- Fuel systems: Gear pumps are used in fuel systems for engines, providing a steady flow of fuel to the combustion chamber.
One of the main advantages of gear pumps is their efficiency. Because the gears mesh tightly, they create very little leakage, which means that almost all of the fluid that enters the pump is delivered to the outlet. This makes gear pumps more efficient than other types of pumps, such as vane pumps or piston pumps, which have greater internal leakage.
However, gear pumps are also known for their noise and vibration. The meshing of the gears creates a pulsating flow, which can cause vibration and noise in the system. This can be mitigated through the use of noise-reducing components, such as vibration dampeners and silencers, or by selecting gear pumps with quieter operating characteristics.
Overall, gear pumps are a versatile and reliable type of hydraulic pump, with a wide range of applications across various industries. Advances in gear pump technology are continuing to improve their performance and efficiency, making them an attractive choice for many hydraulic systems.
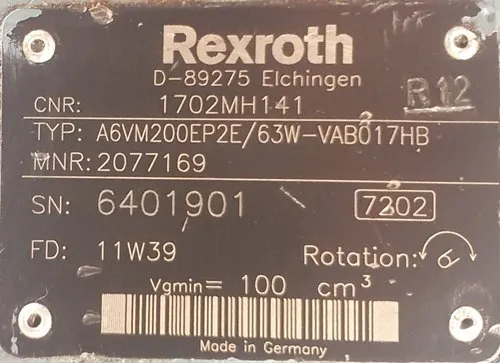
Vane Pumps
Vane pumps are positive-displacement pumps that use a circular rotor with radial slots and vanes to create a vacuum and draw fluid into the pump. As the rotor rotates, the vanes slide in and out of the rotor slots, maintaining contact with the pump casing and creating a seal between the inlet and outlet ports.
The operating principles of vane pumps make them ideal for low-pressure applications where flow rate is more important than pressure. They are commonly used in applications such as power steering systems, transmissions, and hydraulic clutches. They are also used in small fluid power systems and fuel delivery systems.
Advantages of vane pumps include their simplicity, ease of maintenance, and low noise level. They are also able to handle a wide range of viscosities, making them versatile in many different applications. However, they have a lower efficiency compared to other hydraulic pumps, and are not suitable for high-pressure applications.
Vane pumps come in a variety of configurations, including single, double, and triple vane pumps. They can also be classified as fixed displacement or variable displacement pumps. Fixed displacement vane pumps are set to a specific flow rate and cannot be adjusted, while variable displacement vane pumps have an adjustable flow rate.
When selecting a vane pump for an application, it is important to consider factors such as flow rate, viscosity, pressure, and temperature requirements. Proper maintenance and regular inspection of vane pumps is also important to ensure optimal performance and longevity. This includes monitoring for wear and tear of components, replacing worn parts, and ensuring proper lubrication.
In summary, vane pumps are an important type of hydraulic pump with unique operating principles that make them ideal for certain applications. While they may have lower efficiency and are not suitable for high-pressure applications, their simplicity, ease of maintenance, and versatility make them a popular choice in a variety of industries. Proper selection and maintenance of vane pumps is key to ensuring optimal performance and longevity.